The renewable energy produced from all the anaerobic digestion plants operating in the UK, is now equivalent to over a billion tonnes of oil¹. And the food waste that Olleco collects from premises all over the country, is making a significant contribution to that total, and helping to improve both the UK’s energy security and its carbon footprint.
So how are Olleco harnessing this sustainable energy? Who better to ask than Matthew, the Operations Manager at Olleco’s flagship anaerobic digestion plant at Aston Clinton near Aylesbury in Buckinghamshire.
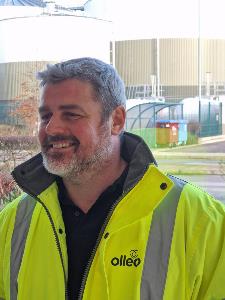
How does the anaerobic digestion (AD) process work?
The AD process takes different sorts of organic materials, such as food waste, and puts them through a plant where they are broken down and “digested” in the absence of oxygen. The process deploys a range of microorganisms that consume the organic materials and change their chemical structures.
As the materials break down, they release methane gas which we harvest and purify. This biogas can then be used to fuel electricity generators or it can be fed directly into the UK Gas Grid where it supplies businesses and homes - reducing our reliance on foreign fossil fuel imports. Once the biomethane has been extracted, we are left with a nutrient-rich organic material known as “digestate” which can be used to replace artificial fertilisers which have a high carbon footprint.
Could you tell us a little bit about the plant you manage?
The AD plant at Aston Clinton is one of the most advanced in the UK. I joined Olleco when it was still at the build stage so I have seen it take shape and helped take it through the ISO 9001,14001 and 45001 accreditation processes. We now accept between two and three hundred tonnes of food waste every day and make enough renewable energy to power the equivalent of 12,000 homes. One of the ground-breaking aspects of the plant was that it is located immediately adjacent to Arla’s largest UK dairy which it supplies with renewable energy. We also process their organic waste streams and water so, together, we form a sustainable loop and contribute to a more circular economy.
So what does a typical day look like at the AD plant?
The AD plant runs 24 hours a day, 365 days a year so it has to be monitored at all times but this can be done remotely. One of us is always on call and we will return to site to investigate if anything unexpected arises and any warnings are triggered. On a normal day, I will arrive at 6am. The first hour of the day is spent checking everything is working as it should be before trucks start arriving with food waste. Typically, each load will be 25 tonnes and they will arrive any time between 7am and 8pm.
People often compare an AD system to a giant stomach and, in some ways, that is true. To keep the micro-organisms inside it working efficiently, you have to maintain a healthy diet. A big part of my role is to analyse that diet and work out what to feed in and when. We go through a pre-acceptance process, so we know the composition of the waste streams we are getting.
We are always on the lookout for waste streams that will optimise the amount of biomethane being produced. I spend quite a bit of my day negotiating with different waste transfer stations to secure the best waste streams for the plant. High calorific values translate into higher performance within the plant.
We also have to ensure that the waste is the right consistency to move through the plant - if it’s too dilute, it won’t produce enough methane but if it’s too thick, it is harder to pump. Something like a large batch of avocado stones can really disrupt the process so we have to be very careful about what we feed into the system.
What led you to work with Olleco?
I trained as a fitter with the Royal Navy and worked on nuclear submarines for 14 years. Coming to Olleco might seem like a leap, but there are more parallels than you might think. An AD plant needs constant attention, adjustment and regular feeding in much the same way as a nuclear reactor. And, of course, there are major safety considerations in an AD plant. You are producing potentially explosive materials that have to be controlled with extreme care and you are moving hundreds of tonnes of material with some pretty heavy duty kit. Safety is the primary concern for Olleco and we are extremely proud of our record which is the result of comprehensive risk assessments and stringent safety procedures. For me, these are second nature, so I am very much at home with Olleco’s zero tolerance approach to risk.
What do you like most about the work?
I love the team I work with. I have been here right from the early days of the build when there were just six or seven of us working on the site. Now there are 18 of us employed here and we are a really tight, efficient team that knows exactly what it is doing and how to get the very best out of the technology we are working with. It has been great overcoming challenges and finding new ways to make the plant run more efficiently and sustainably.
It’s also great to know that I am helping to make the UK’s energy supply more secure and protect us from the influence of foreign fuel fuel supplies.
Do you have a message you’d like to share?
The UK produces over nine million tonnes of food waste every year². By making sure that food that can’t be eaten gets collected and converted into renewable electricity, biogas and fertiliser, you’re doing your bit to tackle the climate emergency.
Want to join our team?